A Living Building Project Journey, Part 1
Setting the Stage
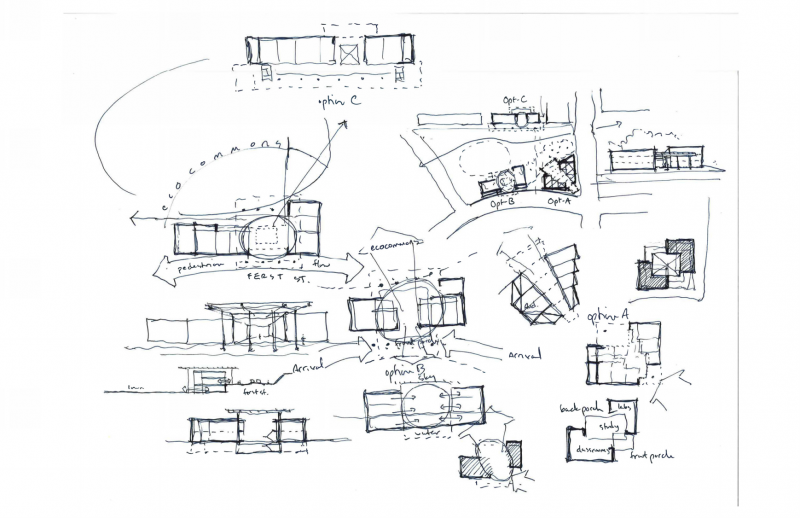
Introduction
After a multi-stage, national selection process which culminated in a two-month ideas competition lead by Georgia Tech, the Lord Aeck Sargent (LAS) / The Miller Hull Partnership (Miller Hull) team was selected to design the first Living Building Challenge (LBC) certified building in the southeast. This is LAS’s second LBC project on the boards and we expect this blog post to be a first in a series documenting the exciting journey.
There are several resources for an in-depth dive into the LBC framework with its Petals and Imperatives but it is worth noting here that the LBC, in the International Living Future Institute’s own words, “is a philosophy, certification, and advocacy tool for projects to move beyond merely being less bad and to become truly regenerative.” It seeks to build an enlightened team of designers, consultants, owners, operators, and occupants who are ever-cognizant of the impact of their decisions and actions leading up to the certification.
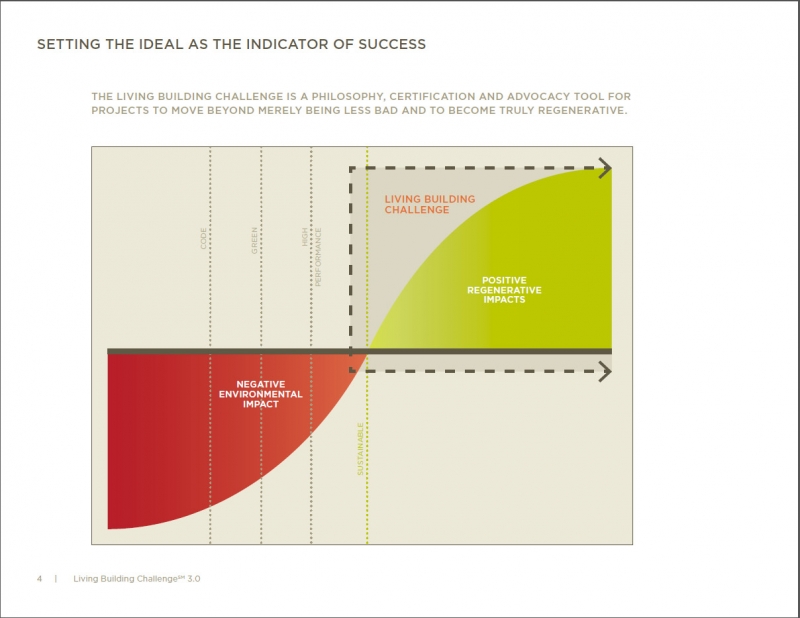
During the design process, no question or concern is too small when it comes to this all or nothing (almost) green building framework with its twenty imperatives. Some early questions and discussions have included:
- Is the most appropriate transect L3 or L4?
- Is a national design team with consultants on both coasts acceptable under the LBC travel distance limitations?
- Would the use of salvaged steel help with the embodied carbon footprint reduction?
- Are there exceptions to the ‘no combustion’ rule when it comes to laboratories?
Beyond detailed considerations of the various program requirements, some broad issues are emerging as high-impact areas. While it is tempting to make this post into a dissertation on the Living Building Challenge, we’ll focus on three issues which illustrate the process to date.
Integrative Design Process
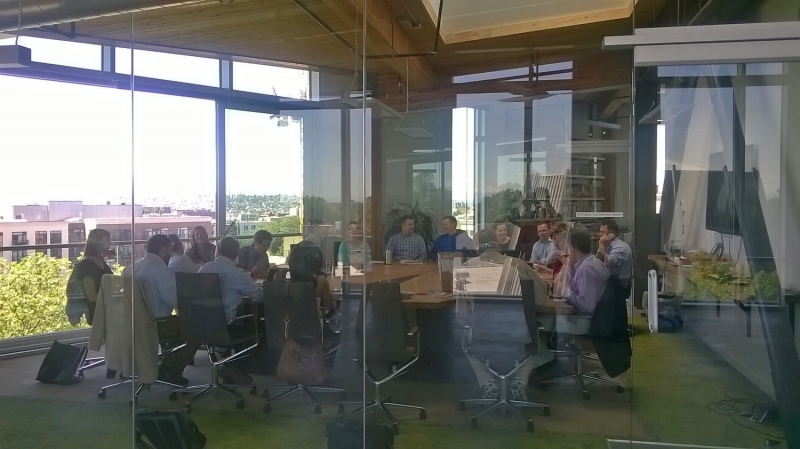
The LBC framework is a forcing function for an integrative design process. It is difficult to accomplish much without the left hand knowing what the right is doing. As we are planning a 2-day “super charrette” and an 8-hour Biophilia charrette, each of our bi-weekly team meetings since the beginning of the project has been a charrette in itself. This has had a transformative impact on the quality of the design process. For example, the quantity and quality of attention given to understanding the site before considering the building itself, and the focus on blurring that boundary, has been extremely exciting.
It’s Very Materialistic
Materials petal requirements, specifically the Red List imperative, will require a new design paradigm. The Red List, with 20+ materials or chemicals to be avoided, encompasses 777 or so chemical compounds once all the variations are taken into account. While there are resources available to marginally help with the Materials petal, we are preparing for:
- deep material research and vetting, and
- deep interaction with manufacturers for information that may not be readily available
Fortunately, there are cautionary tales to learn from: A consultant who is still writing Red List advocacy letters two years into occupancy; an architect who wasted hours looking for lead-free brass door hardware not realizing there was an exception; and a contractor who installed structural insulated panels before noticing the manufacturer had sent SFI-certified version of the product instead of the required FSC-certified.
JUST Certification
The LBC process touches not only design process, but also design team culture . At least one representative from the design team (Architect of Record, Landscape Architect of Record, MEP of Record, etc.) is required to achieve JUST certification. JUST certification aims to “help create a more just, equitable society through disclosure of the business practices of the major organizations” involved in the project. The 22 JUST Label Indicators range from objective measures such as gender diversity to more subjective measures like worker happiness.
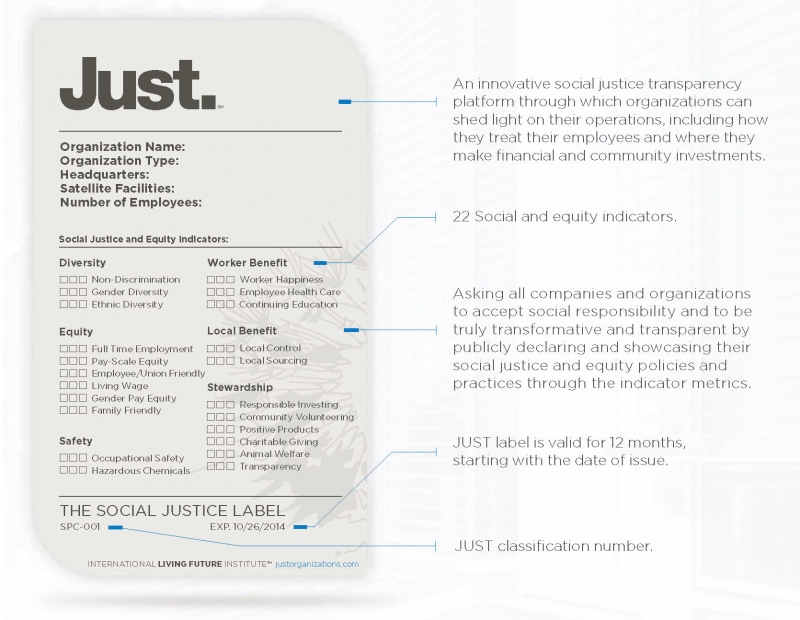
We have formed an internal working group, conducted a gap analysis of our existing policies, and are now developing new policies as needed. It would be an understatement to say that the process has sparked intense conversations.
Conclusion
We’ll continue to share our experience on this journey with future blog posts about this LBC journey. Please share your perceptions of and experiences with the LBC process? We look forward to reading them in the comments section.
Funded through a private grant from The Kendeda Fund, the Living Building at Georgia Tech is expected to become a Living Building Challenge 3.1 certified facility – the built environment's most rigorous and ambitious performance standard. The project’s design and build partners include architects Lord Aeck Sargent in collaboration with The Miller Hull Partnership, construction manager Skanska and design team consultants: Newcomb & Boyd, PAE Consulting Engineers, Uzun + Case, Biohabitats, Andropogon and Long Engineering.
No comments yet